M10/14
Multi Head Weigher M Series
Weigh Range | 5 – 5000g |
Max. Speed | 65 – 120bags/min |
Accuracy | ±0.1 – 2.0 |
Model & Parameters
MS10 | M10 | ML10 | MS14 | M14 | ML14 | |
Application | Small Granule | Normal Granule | Salad | Small Granule | Normal Granule | Salad |
Weigh Range | 5 – 200g | 10 – 1000g | 20 – 3000g | 5 – 200g | 10 – 2000g | 20 – 5000g |
Max. Speed | 65 | 65 | 50 | 120 | 120 | 80 |
Accuracy | ±0.1 – 1.0 | ±0.1 – 1.5 | ±0.1 – 2.0 | ±0.1 – 1.0 | ±0.1 – 1.5 | ±0.1 – 2.0 |
Weigh Bucket | 0.5l | 1.6 / 2.5l | 5l | 0.5l | 1.6 / 2.5l | 5l |
Net Weight | 280kg | 320kg | 500kg | 350kg | 400kg | 900kg |
Machine Structure
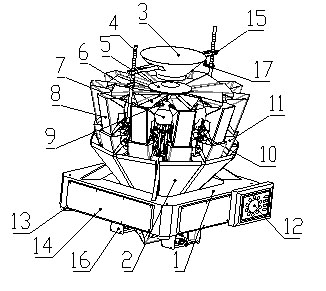
1: Machine Frame | 2: Discharge Chute | 3: In-feed Funnel | 4: Supporting Post |
5: Top Cone | 6: Linear Feeder Pan | 7: Upper Cover | 8: Feed Hopper |
9: Linear Vibrator | 10: Actuator | 11: Weigh Hopper | 12: Touch Screen |
13: Plastic Screw | 14: Base Cover | 15: Sensor Clamp | 16: Timing Hopper |
17:Photo Sensor |
Working Principle
Feeding
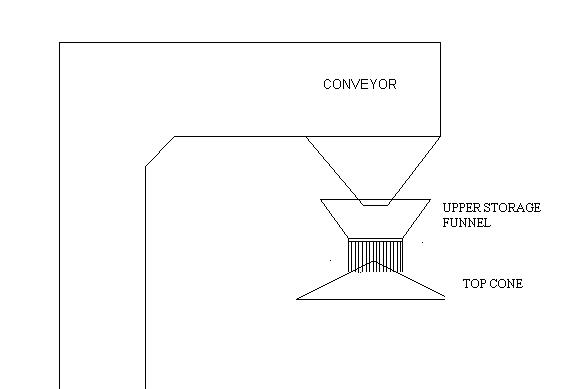
Product is firstly delivered by Conveyor into upper storage funnel, then discharged and distributed to linear vibrator pans with the help of the top cone. Product thickness can be adjusted by adjusting the height of storage funnel post.
Product Distribution and Weighing
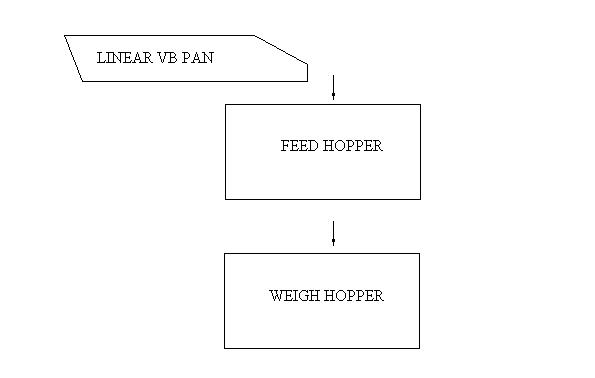
Product is distributed evenly from Top Cone into each Linear Feeder Pan and stored in Feed Hopper. When Weigh Hopper finishes the previous weighing and discharges the combination, the products in Feed Hopper will be dropped to Weigh Hopper to be weighed and combined.
Combination
The machine CPU will process the weight data received from each Weigh hopper, and calculate out numerous qualified combinations which comply with the target weight, then choose the best one to discharge.
The parameters related with “weight in weigh hopper”, ‘AFC’, ‘Main AMP’, ‘Line AMP’, ‘Average Combine Hoppers’, ‘Average Hopper Weight%’.
The parameters related with combination: ‘OPTIMUM’, ‘Combined Hoppers’
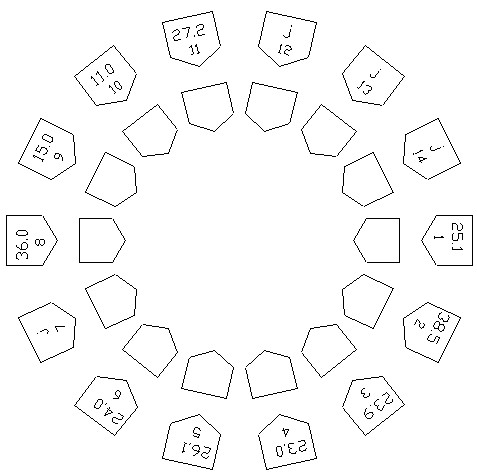
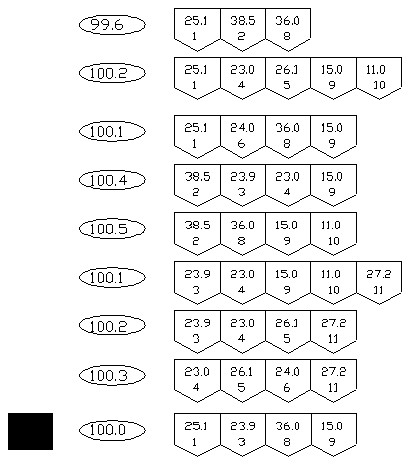
Discharge
There are four ways to discharge weighed products to next equipment:
Working Environment
Temperature: 0 – 40°C
Humidity: 35 – 85%
Power: AC220 ±5V, 50 – 60HZ
Installation place: On rigid, horizontal and no vibration surface.
Earth line: Make sure the machine is connecting effectively to the earth.
Keep away from the disturbing sources.
Food packaging should be operated under aseptic and non-dust environment.
Attention
No bumping or strong pressures on weigh hoppers.
Check and empty the rest product inside the machine before running.
Press Zero to empty hoppers before the first running.
Turn off the power before repairing and cleaning the machine.
When electronic part fails, non-electronic-engineer is prohibited to repair the machine.
Be careful and cautious when cleaning and repairing the machine, because there is certain distance between the weigher and the ground if the weigher is installed on the top of the packaging machine.
Direct current for the connection signals with other equipments (packing machine, conveyor, etc.), should be no more than 30V, the overloading current should be no more than 100mA.
It is prohibited to touch the hopper while the machine is running.